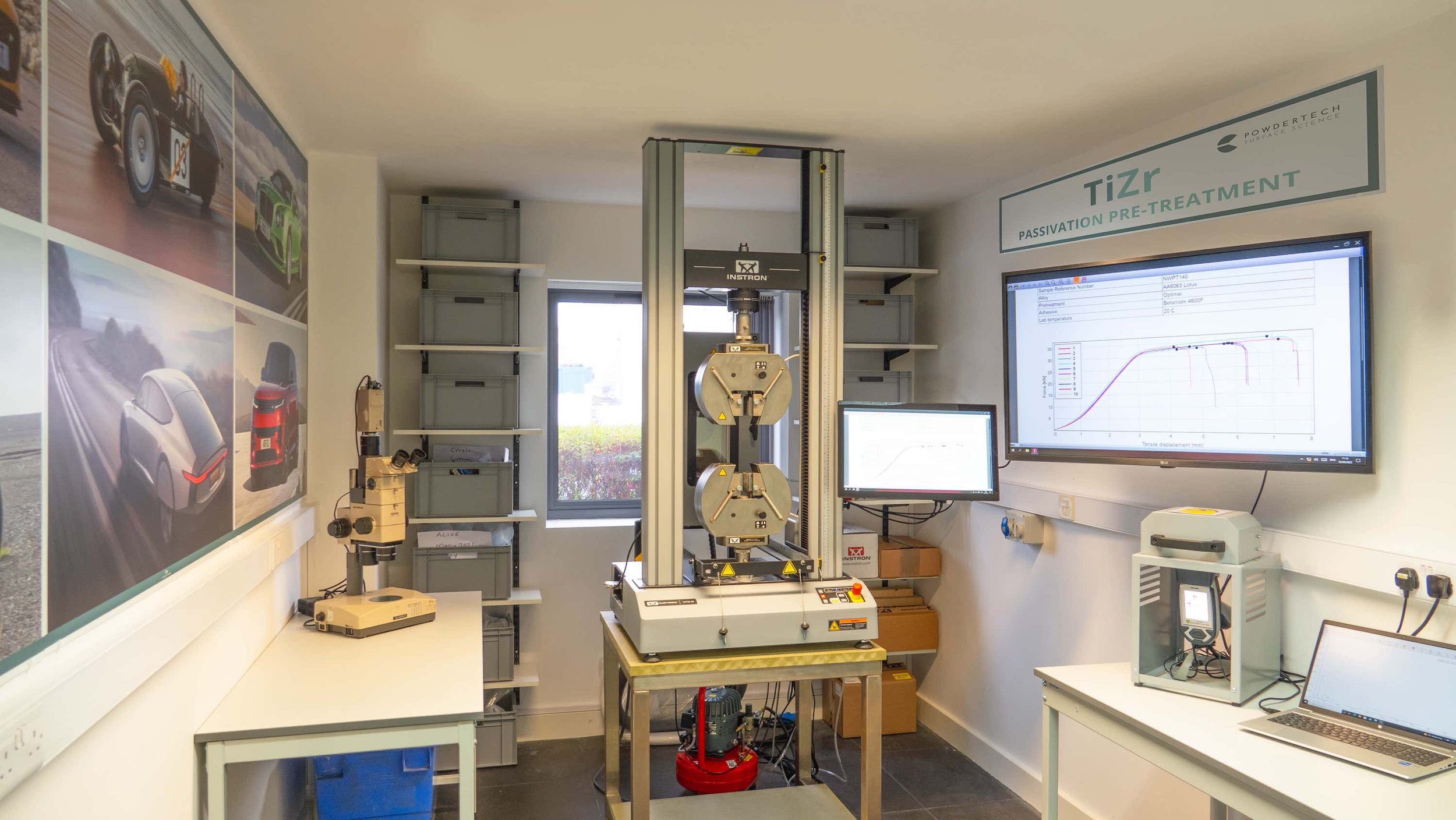
Testing and Development
Testing and development of surface treatments including TiZr pre-treatments and dielectric coatings
Testing, development and managed control of our aluminium surface treatments and powder coating process are core services at Powdertech Surface Science, both for our ongoing client-based processes, coupon testing for clients and research work for OEMs.
Investment in advanced equipment and team expertise
We have the capability and expertise to offer a suite of tests and analytical techniques to probe the properties of a given surface for our clients. This is made possible by our investment in sophisticated equipment to evaluate aluminium surface cleanliness and bonding strengths.
Your project will benefit from our knowledge and expertise which is always at the cutting edge through our participation in key research projects within the industry. We will provide reports, feedback and recommendations to assist product development & process improvement.
All testing, research and development work is done on our site, coordinated by our technical team and overseen by our technical expert ,Dr Nick Welton, who specialises in the science of surfaces and coatings and has been working in the industry for over 25 years.
On-site labs to ensure the highest standards in metal finishing
To measure and control our metal cleaning treatments, TiZr passivation process and powder coating, we have two dedicated surface coating laboratories, a Surface Characterisation Laboratory (dry lab) and a Quality Control Laboratory (wet lab).
For these laboratories we have invested in the latest equipment to accurately measure all aspects during and after surface treatment process. These include
Exact levels of cleanliness of aluminium (and magnesium) surfaces.
Insulating properties of dielectric coatings
Surface composition of aluminum
The strength of bonded metal joints after TiZr passivation
Detection of flaws in surface coating
Daily maintenance of our pre-treatment and coating systems
Aluminium coupon testing services at Powdertech
How can you be certain that TiZr pre-treatment will give you the bond strength and durability that you need?.
At Powdertech Surface Science we provide a range of test services, including the full range of aluminium coupon tests:
adhesion/ cohesion
lap shear
T-peel
tensile
fatigue testing
We can show that our TiZr pre-treatment, also known as TiZr passivation, matches anodising for enhancing aluminium bond strength.
Read our paper on this topic HERE
Whether you require data for your customer or end user, or simply the peace of mind that TiZr pre-treatment will be a suitable and successful choice, our on-site test facilities can provide the reassurance needed.
Instron: Measuring bond strength
We want to be certain that the passivation process we provide is 100% fit for any intended purpose, most especially when it comes to TiZr coating for bonding. We have the capability to optimise our TiZr treatment to meet different specification requirements. This includes ensuring that the bonds achieved following our TiZr conversion coating consistently meet and exceed our customers’ requirements.
We have world leading Instron equipment as part of our testing suite. This is an electromechanical universal testing machine, able to perform a wide range of mechanical tests including tensile, compression, bend, peel, tear, friction, and shear testing. Tests are performed on all the aluminium alloys we work with, from 3xxx series up to 7xxx series, and in all formats, cast, extruded and sheet.
The results of our Instron testing enable us to work with our clients to help them to understand the optimal surface finishing pre-treatment process they need to take their bonding strategies to the next level, and to achieve repeatability going forwards.
The Instron 34TM-50 tests materials in accordance with ASTM, ISO and other industry standards. It has a 50kN load cell and 80mm wide grips, with a thermal chamber capable of reaching 350C.
Instron 34TM-50
Dielectric coatings: Testing surface integrity and insulating properties
The accuracy of the dielectric coating, and insulation properties of the coating are tested and ensured by using three different tests.
Hi-Pot (high potential) testing
This verifies insulation strength and uniformity
Hi-Pot testing is a ‘withstand test’. It measures the breakdown voltage – the threshold voltage at which the initiation of breakdown occurs, electrical insulation no longer functions and current flows. A high voltage is applied to the coated surface and resulting current measured. The objective is that no current should flow.
This process is also valuable for quality control, as it helps identify any inconsistencies or defects in the dielectric coating.
The dielectric strength of a coating is a critical parameter, and hi-pot testing verifies whether the coating can withstand the intended operational voltages. It ensures that the insulation is robust enough to prevent electrical breakdown or short circuits during normal usage conditions.
By subjecting the coating to a high potential, the test ensures that the insulation is uniform across the entire electrode surface, preventing weak points that could lead to short circuits.
Megohmmeter (Insulation Resistance Tester)
The megohmmeter measures the resistance of an insulator which is a key indicator of its ability to prevent electrical leakage.
A high DC voltage is applied to the component and the current flow is measure and converted to a resistance reading (typically in megohms).
Holiday testing - detection of pinholes and defects
This is the ‘continuity’ test and detects pinholes, air bubbles, cracks, or thin spots in the dielectric coating (know as ‘holidays’) that may not be visible through visual inspection alone. Pinholes and thinning could compromise the insulation integrity and potentially lead to short circuits.
The method uses an electrical current that flows through a low resistance path and triggers an alarm (buzzer) when a holiday is detected.
Holiday testing to ensure no flaws in the dielectric coating
Measuring insulation properties of dielectric coating
Surface cleanliness
We use Dyne inks and UV-Fluorescence to measure the level of aluminium surface contaminants and to demonstrate compliance to specifications detailing RFU limits.
Why do we take so much care over this measuring and cleaning prior to powder coating and adhesive bonding?
The simple reason is that surface contaminants, many that can’t even be seen, will impair the performance of any adhesive or coating applied to the metal.
Bond strengths will be unacceptably low, especially in wet environments when surface corrosion can initiate. Battery Electric Vehicles (BEV) are a good example where a high levels of cleanliness in the component structure are vitally important to ensuring the integrity and safety of the battery system.
For powder coating, a poorly cleaned surface can result in coating defects such as fisheyes, inclusions, pinholes and reticulation.
We will always ensure that your metal is clean before any coating is applied.
When Dyne level test fluid is applied to the metal surface, the liquid will either form a continuous film on the surface or pull back into small droplets. They quality of the continuous film will determine the suitability of the surface for coating.
Measuring elemental composition
We have XRF (X-ray fluorescence) capability on-site. This handheld device will give us immediate, lab-quality results from which we can determine the next course of action, allowing us to stay on top of our TiZr passivation quality better than ever.
This is a powerful, non-destructive technique for measuring elemental composition from magnesium (Mg) to uranium (U).
Handheld XRF (X-ray fluorescence) equipment to determine the chemical composition of a sample.
Daily control and maintenance for powder coating systems
The processes and chemicals used in our aluminium surface treatments are measured and tested throughout the day, every day, in our Quality Control Laboratory.
This is to ensure that concentrations, pH levels and cleanliness are optimal and consistent.
Temperatures of the ovens to cure the powder coating are also monitored throughout the day. Coating jobs are preceded by test plates to check the powder coating thickness, gloss level, smoothness, bond strength and colour consistency.
Find out more on our Facility page
Surface Coating Tests Performed
-
Physical Testing
Adhesion
Cross Hatch
PATTI
V Cut
Permeability
High performance adhesion
Impact Testing
Bend Testing
-
Failure Analysis
Root cause analysis
Cross- sectional analysis
Corrosion analysis
Adhesive failure modes
Flaw detection
-
Surface Characterisation
Surface Energy
Surface Cleanliness
Gloss value
Composition of materials
- Microscopy
- Optical
- SEM
-
Environmental Testing
Weathering
Humidity
Corrosion
Thermal Cycling
-
Dielectric Testing
Holiday testing
Hi-Pot testing
Insulation resistance testing
More reasons to choose Powdertech
We carry out a meticulous final inspection - checking dimensions and visual aspects of the parts.
Direct despatch to OEM’s. We are familiar with EDI systems and online booking of transport, direct to end users.
We offer express turnaround in a matter of hours - we are set up for rapid job completion where necessary.
Dedicated warehouse facilities for raw and finished goods.
Can we help you with testing or developing a new surface treatment?
or find out more about our Dielectric, TiZr and INTRICOAT services
More Metal Finishing Services