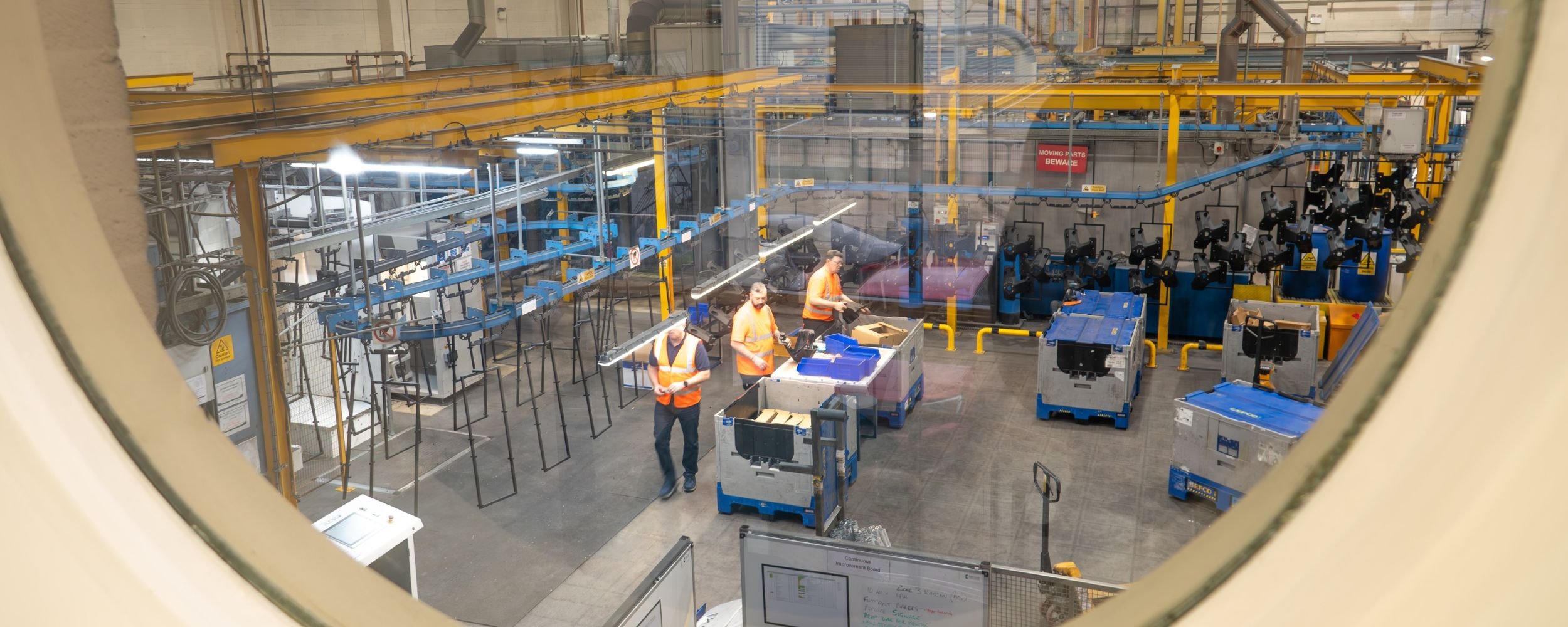
Our Facility
Investment in advanced equipment and team expertise
We continually invest in our facilities to ensure a powder coating service that excels in quality, consistency, and adaptability to evolving industry demands. Additionally, our team includes leading expertise in surface treatments, led by our Technical Manager, Dr. Nick Welton.
Systems for metal pre-treatment and powder coating
Automated horizontal powder coating line for parts up to 4m in length
Automated vertical powder coating line for smaller components of up to 1.2m in length
6-axis Lesta robot for refining inaccessible areas, replacing manual touch up.
GEMA OptiCentre powder management system. With GEMA’s SIT dense phase powder pumps
A smaller coating booth for prototype and sample work. This has a dedicated box oven that can also accommodate sections up to 4 metres in length
Two 13-stage immersion pre-treatment lines, fully programme logic controlled. This offers both a high degree of control and the ability to handle high volumes
7-stage pre-treatment pilot line. This providing in-house capability to test and develop new pre-treatments
Dedicated facility for INTRICOAT masking and powder coating
Machined components are becoming ever more complex together with an increasing requirement for finishes with premium aesthetics.
INTRICOAT provides a hands-on service for intricate aluminium components, utilising masking schemes designed on our CAD systems. We have invested in a dedicated separate facility, located within our plant, to be used exclusively for masking, jigging and coating these components in low volume.
CAD – using AutoDesk Fusion 360 - This enables us to upload design drawings and develop customised making schemes. We can visualise the process and determine how elements of the design will interact. The software allows us to evaluate surface area, the component mass, it’s centre of gravity and other data.
Gema Classic Line Spray Booth.
Gema OptiFlex Pro B spray gun - The Optiflex Pro B Spray powder coating device from Gema is the perfect solution for coatings that require stable powder output as well as easy and quick colour changes.
Jigging – around 20% of our jigging is custom made to suit particular components.
Airflow Box Oven with a unique high efficiency thermal design - We achieve superior production results due to very uniform temperature and the innovative ‘high volume low pressure ‘ hot air circulation system
Masks – these need to be cut precisely, typically to 0.01mm.We use a combination of Greentree masks and our own 3Ddesigns produced by Quickparts.
Size range of components for masking. The smallest component that we have masked recently had a diameter of 12mm. The largest parts receiving INTRICOAT service are 660mm x 600mm x 280mm, weighing 70kg.
Advanced laboratories for bond strength testing, surface composition testing and quality control
Instron 34TM-50 for bond strength testing
.
We have two dedicated surface coating laboratories, a Surface Characterisation Laboratory (dry lab) and a Quality Control Laboratory (wet lab). These work in conjunction in order for us to test:-
Bond strength following TiZr passivation process
High potential testing, used for dielectric coatings
Surface characterisation and cleanliness
The ongoing quality control of our pre-treatment and coating systems
Bond strength testing
Instron 34TM-50 for bond strength testing
This is an electromechanical universal testing machine, able to perform a wide range of mechanical tests including tensile, compression, bend, peel, tear, friction, and shear testing.
-
Tests are performed on all the aluminium alloys we work with, from 3xxx series up to 7xxx series, and in all formats - cast, extruded and sheet.
The Instron 34TM-50 tests materials, components, and products in accordance with ASTM, ISO and other industry standards. It has a 50kN load cell and 100kN 80mm wide grips, with a thermal chamber capable of reaching 350C.
Defelsko Positest AT-A to test pull-off adhesion
Our laboratory has the capability to test pull-off adhesion to ASTM D 4541 using Defelsko Positest AT-A as well as number of other methods for evaluating surface performance of substrates.
Testing dielectric coatings
In order to ensure that the dielectric coatings we apply meet the required insulation properties we use three tests:
Holiday tester – used to identify areas where the coating might be too thin, or where minute pin holes may have occurred. Any failure in the integrity of the coating would result in unsafe leakage of current.
Hi-Pot tester - this measures the breakdown voltage – the threshold voltage at which the initiation of breakdown occurs, electrical insulation no longer functions and current flows. A high voltage is applied to the coated surface and resulting current measured. It tests the dielectric strength of insulation by applying a voltage higher than the device's normal operating voltage to see if the insulation breaks down.
Megohmmeter (Insulation Resistance Tester) - the megohmmeter measures the resistance of an insulator which is a key indicator of its ability to prevent electrical leakage. A high DC voltage is applied to the component and the current flow is measure and converted to a resistance reading (typically in megohms).
Testing aluminium surface cleanliness
At Powdertech we are clear that our role goes further than providing exemplary aluminium surface treatments. We want to be certain that the TiZr and powder coating processes we provide are 100% fit for any intended purpose.
In order to achieve the best possible results, we need to ensure that the metal is clean to start with. We use:
Dyne inks – to reveal surface energy levels
RFU Fluorescence Unit - to inspect the cleanliness of surfaces
XRF tester – to measure the composition of materials
Quality Control
The processes and chemicals used in our aluminium surface treatments are measured and tested throughout the day, every day, in our Quality Control Laboratory. This is to ensure that chemical concentrations, pH levels are optimal and consistent, and that the tanks are clean.
Temperatures of the ovens to cure the powder coating are also monitored throughout the day. Coating jobs are preceded by test plates to check the powder coating thickness, gloss level, smoothness, bond strength and colour consistency.
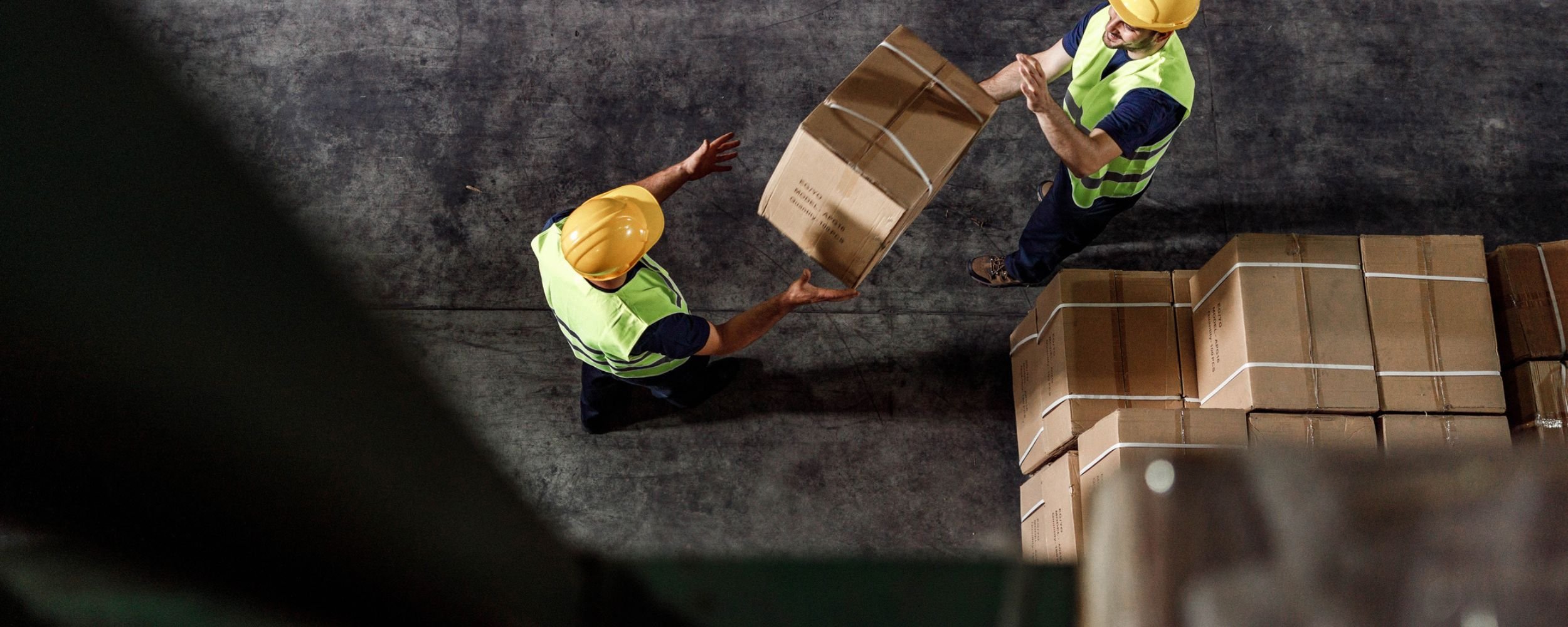
Warehouse Facilities
We have a dedicated warehousing facility in Bicester, providing 10,000sqft of space for storage of raw and finished goods if required.
More from Powdertech Surface Science
-
Our Team
-
Our Facility
-
About Powdertech
-
Sustainability